EVERHEAL-Injection Dispensing Systems
27 Mar.,2025
The following is a news summary of Injection Dispensing Systems:
Attention is drawn to Injection Dispensing Systems. The main equipment of the preparation unit is the dosage tank, which mainly addresses the issue of mixing uniformity. There are regulatory requirements for pharmaceutical dosing tanks, such as pressure measurement methods, and the design of atmospheric pressure vessels.
Formulation unit
• The main equipment of the preparation unit is the dosage tank, which mainly solves the problem of mixing uniformity.
• Structure of dosage tank: Usually, the dosage tank adopts the structure of oval head at both ends of cylindrical shape. It consists of tank body (cylinder), upper and lower heads, legs (lugs), manhole (feeding port), process pipe port, tank bottom valve (discharge port), stirring (upper mechanical stirring, lower magnetic stirring), jacket or companion pipe jacket, steam or cooling water inlet and outlet, and heat preservation.
• Accessories of dosing tank: breather, cleaning ball, liquid level
detection (weighing), safety explosion relief, pressure detection,
temperature detection, sampling and electrical control.
Regulatory Requirements for Pharmaceutical Dosing Tanks
• Basic requirements/reference to JB/T200742005
• The design of dosage tanks belonging to pressure vessels shall comply with the relevant provisions of GB150;
• Definition of pressure vessel: the maximum working pressure is greater than or equal to 0.1Mpa (gauge pressure), the volume is greater than or equal to 30L, the gas, liquefied gases and the maximum working temperature is higher than or equal to the standard boiling point of the liquid of the stationary or mobile containers; holding working pressure is greater than or equal to 0.2Mpa (gauge pressure), and the pressure and volume multiplied by the product of the gas is greater than or equal to 1.0Mpa.L, the gas, liquefied gases and the standard Boiling point equal to or then 60 degrees of the cylinder, medical oxygen tank.
• Gauge pressure: pressure measurement starting from atmospheric pressure.
• Absolute pressure: pressure measurement starting fromabsolute vacuum.
• The design of dosage tanks belonging to atmospheric pressure vessels shall comply with the relevant provisions of NT/T47003.1-2009;
Manufacturing requirements for pharmaceutical
dosing tanks
• Parts in direct contact with materials should be made of austenitic stainless steel which does not react with materials;
• Seals are made of non-toxic, odourless, non-shedding particles, heat-resistant and corrosion-resistant materials;
• Insulation materials in the dosing tank should comply with the regulations, mainly cannot contain chlorine;
• The dosage tank should have on-line cleaning and on line sterilisation function.
• The surface of the tank is smooth, no dead corner, easy to clean and sterilise, and the surface roughness Ra of the surface in contact with the material should be no more than 0.4um.
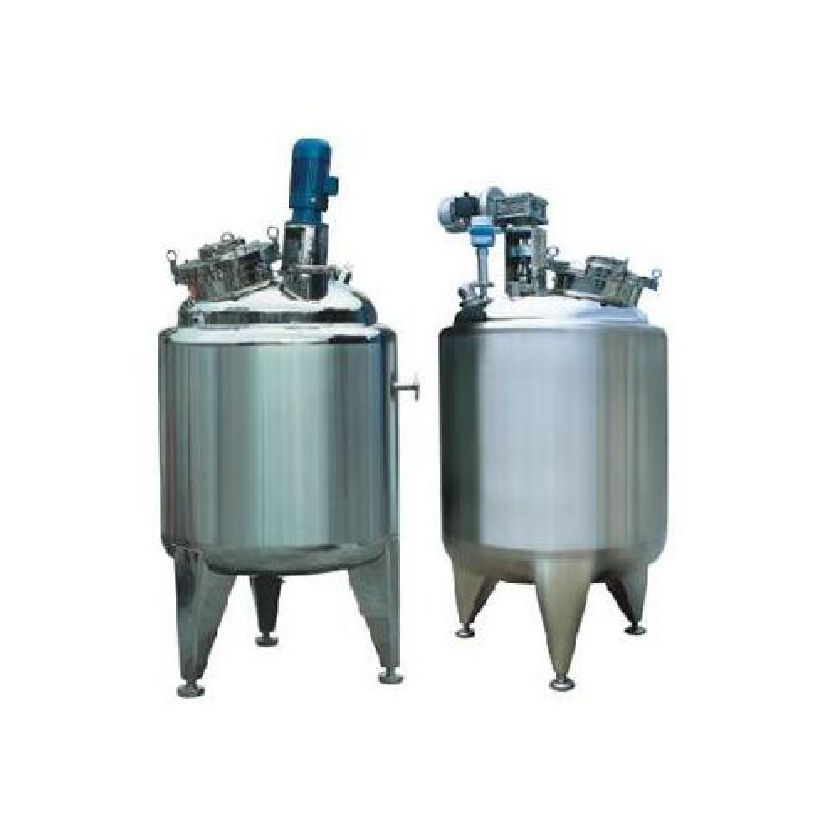
Conveying unit
• The main equipment of the conveying unit is a conveying pump, which can also be powered by compressed air.
• Currently used transfer pumps are mainly centrifugal pumps, diaphragm pumps, rotor pumps, screw pumps, of which more than 80 per cent are stainless steel sanitary centrifugal pumps.
• The use of spiral surface type pump casing, wetted part of the stainless steel surface polishing only Ra value of less than 0.5um or better.
• In order to ensure that the whole system can be drained, ASME BPE standard recommends that centrifugal pump outlets should not be installed with any check valves.
• The impeller is preferred to the full open impeller, which belongs to one-time forging moulding, with simple internal structure, easy to clean, and in full compliance with GMP requirements.
• Without special requirements, the mechanical seal adopts single end face machine seal.
• The bottom of the chamber is equipped with a low-point discharge port.
Dosing tank mixing
Mechanical mixing:
• The sealing of the mixing shaft should adopt sanitary sealing structure, and there should be reliable measures to prevent
leakage and contamination of drugs.The connection between the stirring shaft and the stirrer should be easy to disassemble and
clean, and the structure of the stirrer should have no dead space that is not easy to clean.The surface roughness Ra of the agitator should be no more than 0.4um.The radial oscillation at the shaft seal at the upper end of the stirring shaft after the assembly of the stirring device should be no more than 0.5mm.
Magnetic stirring
• The magnetic stirring system should be fully closed and without leakage.The oscillation of the stirring paddle at the upper end of the magnetic stirring shaft should be no more than 0.2mm.The dosing tank should run smoothly, no abnormal rattling in the
transmission system, and the noise of load operation should be no more than 75 dB.
• Comparison of stirrers; mechanical stirring can transfer large torque, high efficiency, but there is a risk of leakage, and not easy to clean; the lower magnetic stirring is installed at the bottom of the tank, which can stir the low liquid level materials,
especially suitable for high value-added products; no mechanical seal, no risk of leakage, and easy to clean. The disadvantage is that the torque transmitted is relatively small.
Dosing tank
Magnetic Stirrers
Conveying unit
• The main equipment of the conveying unit is a conveying pump, which can also be powered by compressed air.
• Currently used transfer pumps are mainly centrifugal pumps, diaphragm pumps, rotor pumps, screw pumps, of which more
than 80 per cent are stainless steel sanitary centrifugal pumps.
• The use of spiral surface type pump casing, wetted part of the stainless steel surface polishing only Ra value of less than 0.5um or better.
• In order to ensure that the whole system can be drained, ASME BPE standard recommends that centrifugal pump outlets should not be installed with any check valves.
• The impeller is preferred to the full open impeller, which belongs to one-time forging moulding, with simple internal structure, easy to clean, and in full compliance with GMP requirements.
• Without special requirements, the mechanical seal adopts single end face machine seal.
• The bottom of the chamber is equipped with a low-point discharge port.
• Concentrated preparation - transfer pump - titanium rod filtration and decarburisation - diluted preparation - transfer pump - pre-filtration - fine filtration - dispensing tank;
• The liquid can be circulated back to the concentrated mixing tank after being filtered and decarburised by titanium rods after concentrated mixing;
• After diluted preparation, the liquid can be filtered to the filling tank and then circulated back to the diluted preparation tank;
• Compressed air, nitrogen and other gases require sterilisation filters;
Basic process of liquid preparation
• Pure steam filter cartridges are high temperature resistant;
• The pH value can be monitored and displayed online, and the pH meter can be disassembled to withstand high-temperature
sterilisation;
• The pipeline size and pressure should be reasonably designed according to the above requirements, and some instruments,
pipeline valves and control components should be designed and configured according to the actual requirements;
• The main equipments of the pharmaceutical liquid dispensing system are composed of dissolving tank, thick dispensing
irrigation, thin dispensing irrigation (all kinds of irrigation are equipped with stainless steel stirring, magnetic stirring, etc.),
conveying pump, weighing instrument, liquid level meter, all kinds of filters and other units.
• Dosing equipment with heating, cooling and heat preservation, stirring and other functions.
• Dosing tanks and other contact with the liquid part of all stainless steel manufacturing, smooth surface.
• The dosing tank and piping system are required to be free of residue and dead space;
• Stirring speed: it can be considered that the speed can be controlled to ensure that the drugs are dissolved within the specified time, and so on;
• Temperature control: the speed of temperature rise and fall can be controlled, with heating and heat preservation functions, so that the material is at the best temperature;
• Instrument calibration: to ensure accurate operation;
• Weighing calibration: feeding materials accurately;
• Self-rotating cleaning: should ensure that the cleaning is thorough, no dead corner;
Dosing equipment concerns in validation
• Jacketed (fed with steam or cooling water);
• Mechanical sealing: reliable, ensuring no pollution;
• Vessel insulation: high temperature resistant, anti-aging, nonshedding material;
• Product mixing uniformity.
Antibacterial filtration(regulation)
Code for Quality Management of Pharmaceutical Manufacturing
2010 Edition Appendix 1: Sterile Drugs
• Article 90 The final sterilisation process shall not be replaced by a decontamination filtration process for products that can be
finally sterilised. If the drug product cannot be sterilised in its final packaging container, a sterilising filter of 0.22um (smaller or of the same filtration efficacy) may be used to filter the drug solution into a pre-sterilised container. Since sterilisation filters do not remove all viruses or mycoplasmas, heat treatment may be used to compensate for the lack of sterilisation filtration.
• Article 91 Sterilisation filtration carries the greatest risk compared to other methods of sterilisation, therefore it is advisable to install a second sterilised sterilisation filter to filter the liquid once more. The final sterilising filter should be as close as possible to the filling point.
• Article 92 Filters should be as fibre-free as possible. Filters containing asbestos are strictly prohibited. Filters shall not adversely affect the quality of the product by reacting with the product, releasing substances or adsorbing them.
• Article 93 Immediately after use, the integrity of a sterilising filter shall be checked and documented using an appropriate method. Commonly used methods are the bubble point test, the diffusion flow test or the pressure hold test. The filtration process shall be validated, and the validation shall include the determination of the time required to filter a given volume of medicinalsolution and the pressure on both sides of the filter. Any apparent deviation from normal time or pressure shall be recorded and investigated, and the results of the investigation shall be filed in the batch record.
• Article 94 Filters of the same size and type shall be validated to determine the time limit for their use.
We were established by foreign trade staff after studying from overseas in 2008, the team was composed by a number of industry elite as rich experienced internet operators, foreign trade staff, English translators,web designers and web development engineers etc.